AKD Emulsion
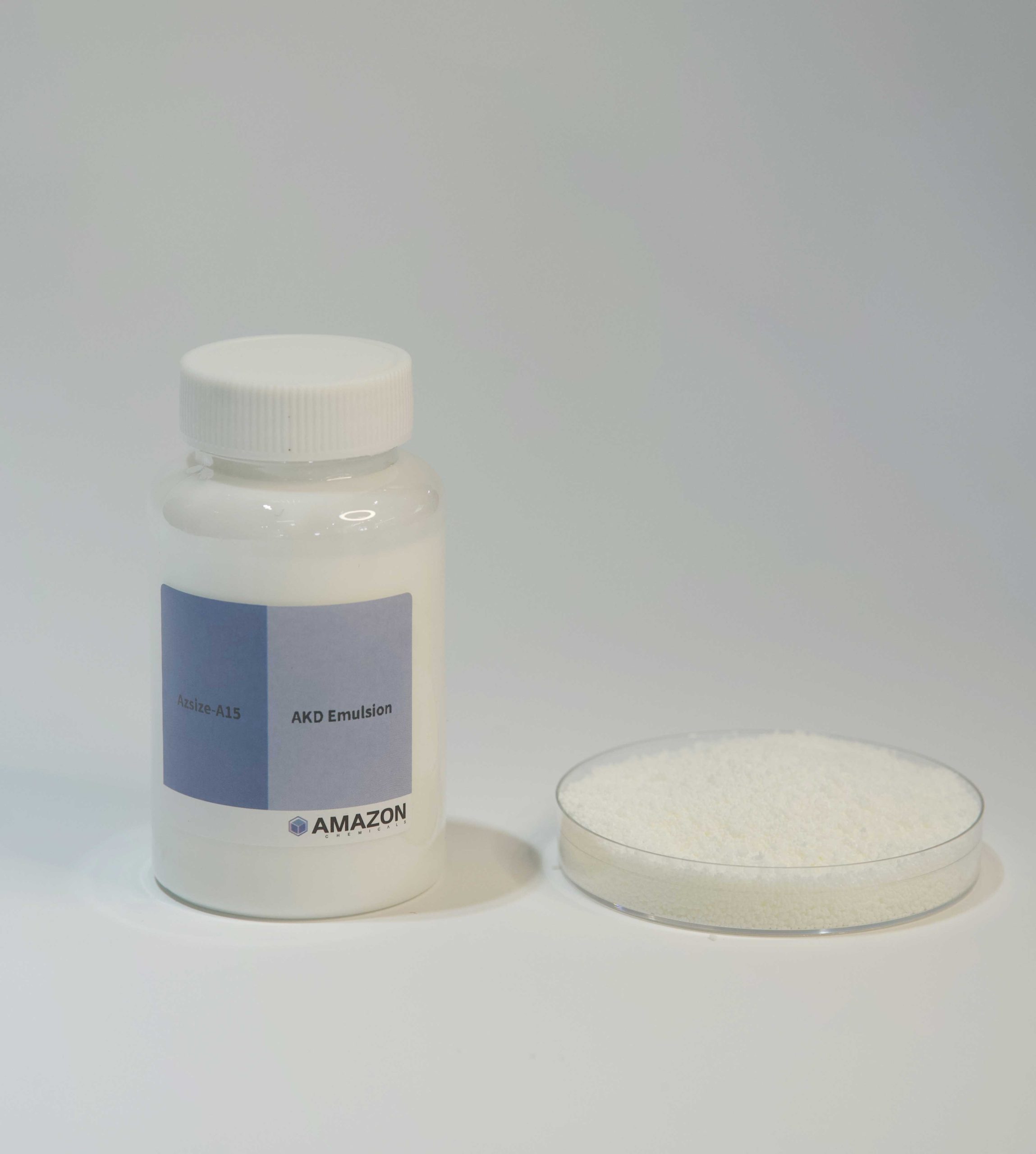
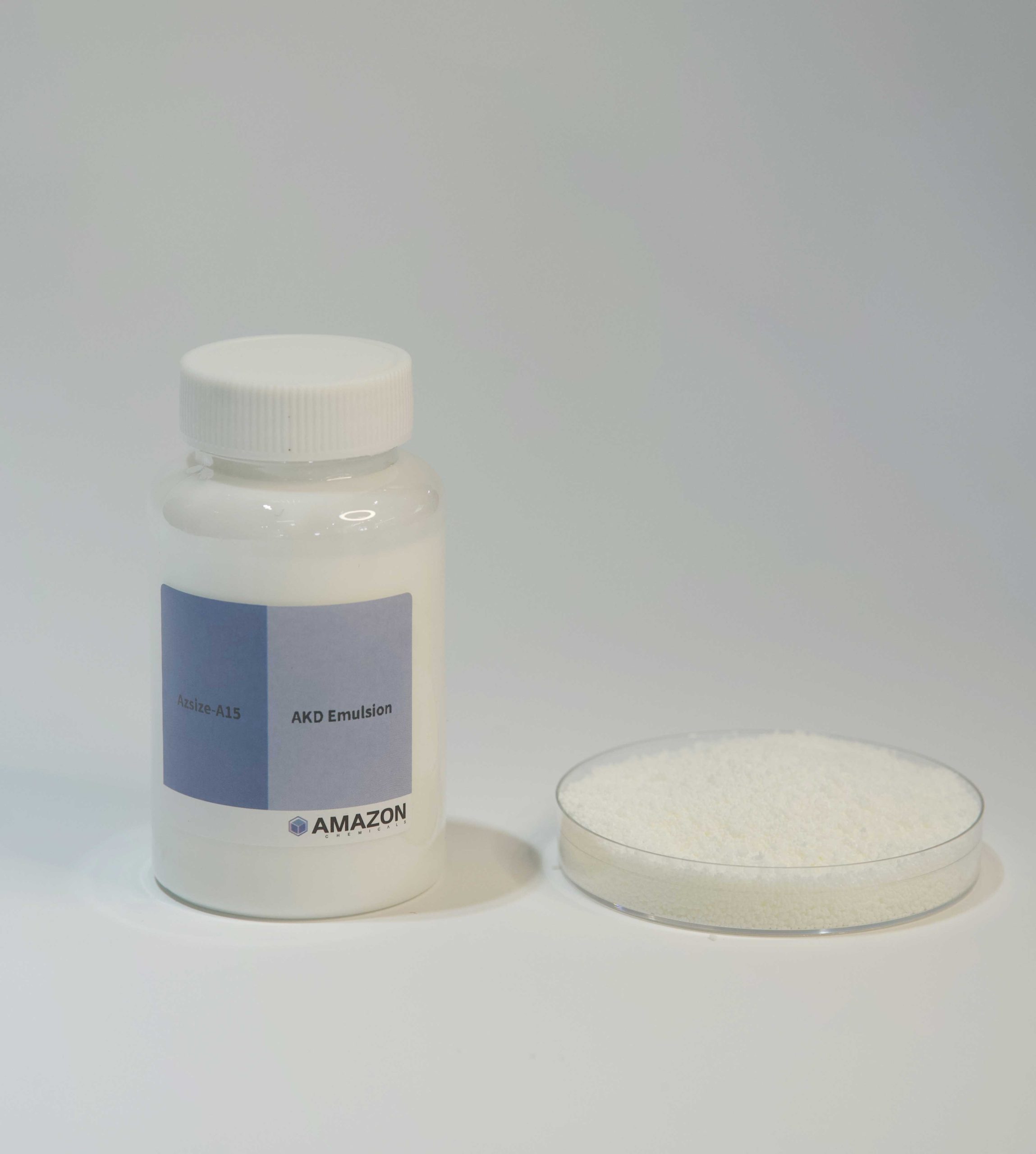
Efficient solution for paper sizing: AKD Emulsion
The Azsize® series is a highly efficient alkyl ketene dimer (AKD) emulsion that reacts directly with cellulose to provide sizing. It is specifically designed to enhance drainage and optimize sizing efficiency in most papermakingsystems. The emulsion is formulated to work effectively with most retention systems and other additives currentlyused in the papermaking industry.
Product Name | Azsize® A15 | Azsize® A18 | Azsize® A20 | Azsize® A25 |
Appearance | Milky white liquid | Milky white liquid | Milky white liquid | Milky white liquid |
Ionicity | cationic | cationic | cationic | cationic |
Solid Content (%) | 15±0.5 | 18±0.5 | 20±0.5 | 25±0.5 |
pH Value | 2-5 | 2-5 | 2-5 | 2-5 |
Viscosity (cps) | <50 | <50 | <50 | <50 |
Application
- The product can be directly add to the thick pulp, or add to the mixing chest after diluted. A dual retention system with cationic starch and polyacrylamide is recommended. This combination ensures optimal sizing efficiency and paper quality, improving the paper’s water resistance and ink absorption.
Packaging and storage
- 200kg PE drums; 1050kg IBC tanks.
- Store in a dry, cool and well-ventilated place, avoid storing in the open air, at room temperature. (4-30℃ indoor cool place)
- Shelf life: 3 months.
Related Research Development
1. Introduction Sizing is a crucial step in the papermaking process. Traditionally, rosin-based sizing—also known as acidic sizing—was commonly used. […]
I. AKD Wax Powder Synthesis Process 1. Chemical Reaction Pathway Starting with stearic acid as the raw material, stearoyl chloride […]
Referring to the Complexity of AKD sizing problem, today it is mainly about the separation and analysis of AKD (unbound […]
To begin with, let’s talk about the complexity of AKD sizing problem from the perspective of interaction. We know that […]
Related News
Between 2022 and 2029, the global barrier coated papers market is estimated to grow at a CAGR of 4.5 percent, […]